Welcome to My Blog!
Before we dive into the content, I’d love for you to join me on my social media platforms where I share more insights, engage with the community, and post updates. Here’s how you can connect with me:
Facebook:https://www.facebook.com/profile.php?id=61576230391049
Now, let’s get started on our journey together. I hope you find the content here insightful, engaging, and valuable.
Table of Contents
Introduction
When planning an industrial electrical infrastructure, one of the most common dilemmas engineers and facility managers face is this: Cable Tray vs Conduit — which system works better? which system works better? Discover the key differences between cable tray vs conduit for industrial wiring.
What is a Cable Tray? Key Advantages and Types Explained
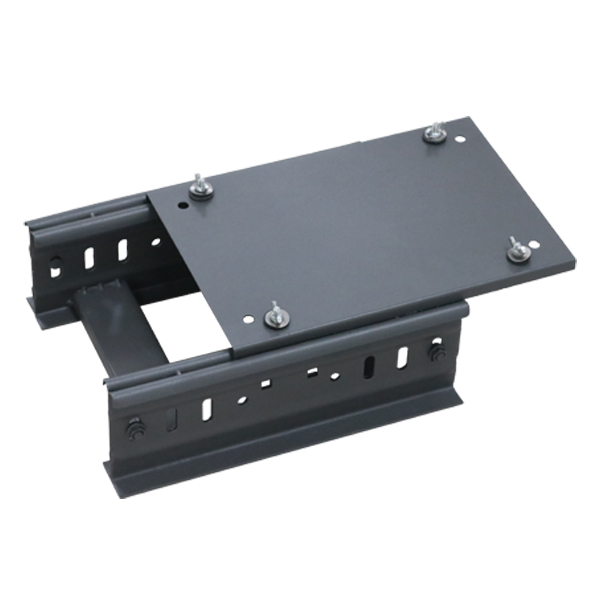
A cable tray is a mechanical support system used to safely route and protect insulated electrical cables, commonly found in industrial settings. Think of it as the “highway” for your power and control wiring — providing physical support, proper spacing, and superior ventilation.
Advantages of Cable Tray Systems
- Quick Installation: No need to thread or bend like conduit systems.
- Ease of Maintenance: Visual inspections and repairs are straightforward.
- Flexible Expansion: Easily add, remove, or reroute cables.
- Cost-Effective: Reduces labor and material costs over time.
- Thermal Management: Better airflow minimizes heat buildup and risk of cable overheating.
According to data from Industrial Wire Systems Journal (2023), facilities using cable trays reported a 30–45% reduction in cable installation time compared to those using traditional conduit systems.
What is Conduit and Where is It Still Applicable?
A conduit is a rigid or flexible tube used to enclose and protect electrical wires. It’s a completely enclosed system that’s been traditionally used for underground runs, outdoor exposure, and environments with extreme hazards.
Types of Electrical Conduits
- Rigid Metal Conduit (RMC): Strong but heavy and expensive.
- Intermediate Metal Conduit (IMC): Lighter than RMC, moderately priced.
- Electrical Metallic Tubing (EMT): Common in commercial settings; easy to bend.
- PVC Conduit: Lightweight and corrosion-resistant, best for low-impact zones.
Disadvantages in Industrial Environments
- Difficult to scale as system grows.
- Heat dissipation is poor, often requiring cable derating.
- Labor-intensive installation increases project timelines.
- Complex maintenance—cables aren’t easily accessible.
Cable Tray vs Conduit: Comparative Table for Industrial Applications
To help you visualize the differences, here’s a quick comparison:
Feature | Cable Tray | Conduit |
---|---|---|
Installation Time | Faster (20–40% less labor) | Slower due to bending/threading |
Maintenance | Easy (open access) | Difficult (requires disassembly) |
Expansion & Upgrades | Simple cable additions | Requires system rework |
Ventilation | Excellent airflow | Poor — may cause overheating |
Cost (Long-term) | Lower | Higher due to labor/materials |
Suitability for Heavy Cables | High (especially ladder tray) | Moderate to High (with effort) |
Flexibility | Highly flexible routing | Rigid paths, hard to modify |
Why Cable Tray Systems Are Better for Industrial Facilities
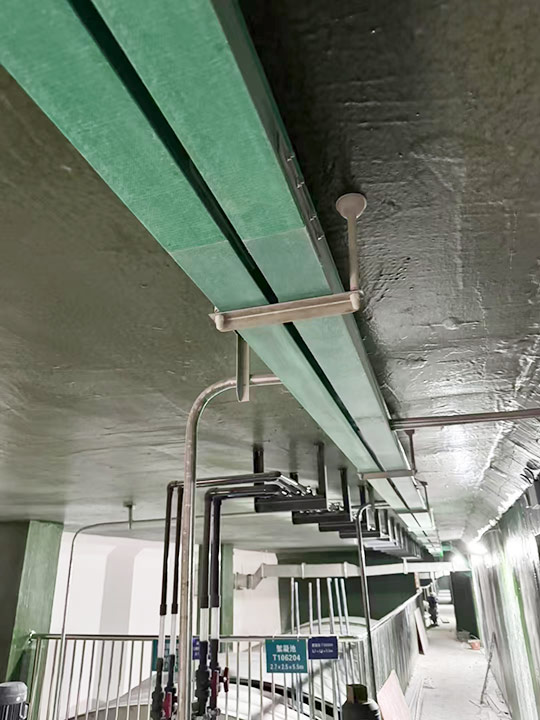
Let’s get specific. Industrial facilities — such as food processing plants, mining operations, and refineries — demand robust, flexible, and accessible cabling systems.
Lower Total Cost of Ownership
Initial cable tray material costs may be similar to conduit. However, labor costs for conduit can exceed 40% of your budget. Cable trays install faster and reduce costly skilled labor requirements.
Reduced Downtime During Maintenance
Need to trace a control wire or replace a damaged power line? With cable trays, you can visually inspect and address issues without removing covers or disassembling anything.
Easier Compliance with Regulations
Cable trays meet safety standards such as:
- IEC 61537 (International cable tray standards)
- NEC Article 392 (widely adopted in industrial design codes)
Conclusion
When it comes to Cable Tray vs Conduit, the clear winner for industrial electrical systems is the cable tray. It’s more efficient, cost-effective, and scalable — making it ideal for today’s complex and ever-evolving production environments.
At Yidian, we help you design and implement cable tray systems tailored to your facility’s needs. Whether you’re working in heavy industry, refining, manufacturing, or power generation — we’ve got the expertise and products to support your success.
📞 Ready to build a smarter, safer electrical system? Contact Yidian for expert consultation and premium-grade cable tray solutions.
FAQ
Are cable trays safe for outdoor or corrosive environments?
Yes, with the right materials. For outdoor or corrosive areas, use hot-dip galvanized or stainless steel cable trays. Yidian offers both.
Can I use both cable trays and conduits in the same facility?
Absolutely. Many facilities use conduits for underground or hazardous zones, and trays for all accessible areas.
What’s the maximum cable load a cable tray can carry?
That depends on the tray design and material. Ladder trays can typically support loads up to 200 kg/m. Always check manufacturer specifications.
Do I need special certifications to install cable trays?
While not always mandatory, working with certified installers ensures compliance with electrical codes and enhances long-term safety.
How often should cable trays be inspected?
Ideally, conduct inspections quarterly, especially in environments with high heat, vibration, or exposure to chemicals.